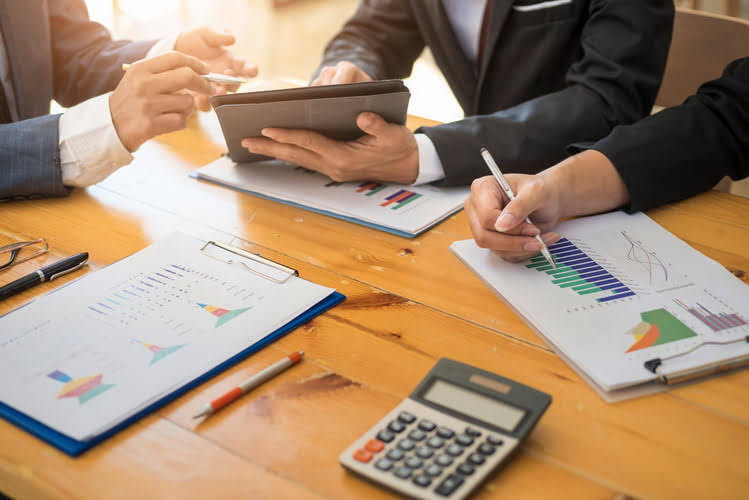
In case you’re spending too many resources on a task or project, the option to set budgets in Clockify will give you a detailed insight into how you can better balance those resources. There are other notifications you can receive by email or in the tool to alert you about activity and task reminders. Our collaborative platform lets you share files and comments with everyone no matter where or when. There are also workflow automation and task authorization features to free up your workers to focus on what matters without jeopardizing quality.
How to calculate manufacturing overhead cost
Simply, totaling the Overhead Costs either for the factory or for various divisions for your business is not sufficient. It is important to assign these Overhead Costs to various products, jobs, work orders, etc. This is because advertising helps to reach out to the potential customers who would be interested in buying your bakery products.
- If the base does not accurately reflect the way overhead is incurred, it can lead to mispriced products and misguided strategic decisions.
- The term fixed manufacturing overhead refers to all factory overhead costs that do not depend on the production volume of a manufacturing business.
- Clockify is a time tracker and timesheet app that lets you track work hours across projects.
- First, we’ll give you a basic understanding of manufacturing overhead costs.
- Combining her knowledge of multiple disciplines, she seeks to help others optimize their work-life balance, which she believes is the key to minimizing stress.
- These costs can be fixed, such as rent, or variable, such as transport costs.
Overhead Cost Examples
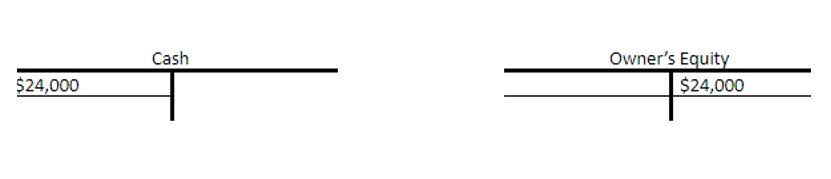
For example, the cost of packaging materials used to package a specific product is product-level overhead. The fixed component of the labor cost is the salary of the supervisor who oversees the production process. The variable component of the labor cost is the wages is shipping cost manufacturing overhead of the workers who directly produce the t-shirts. First, it helps businesses to understand how their costs will change as production or activity levels change. This information can be used to make informed decisions about pricing, production planning, and budgeting.
- Businesses can effectively track and manage semi-variable overhead costs by using detailed accounting software that can separate and categorize these costs accurately.
- Semi-variable manufacturing overhead costs can eat into profits if not managed carefully.
- As a result, the steel manufacturing company was able to achieve a 10% reduction in manufacturing costs and save €1 million (approximately $1.7 million) annually.
- This method is used when there is no particular pattern to the asset’s loss of value.
- To implement ABC, businesses first need to identify all of the activities that consume overhead costs.
- This is because there can be a permanent change in the fixed expenses over a long period of time.
What is Manufacturing Overhead Cost?
Yet these and other indirect costs must be allocated to the units manufactured. As their names indicate, direct material and direct labor costs are directly traceable to the products being manufactured. Manufacturing overhead, however, consists of indirect factory-related costs and as such must be divided up and allocated to each unit produced. For example, the property tax on a factory building is part of manufacturing overhead.
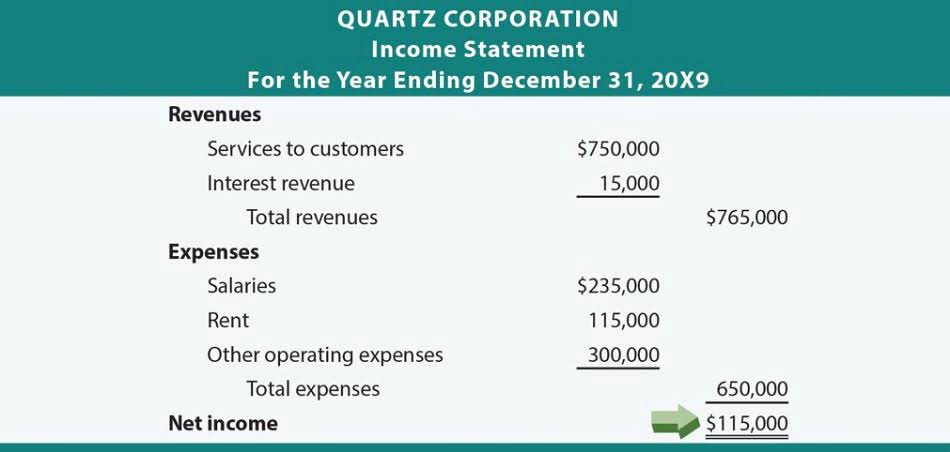
Download our free production schedule template for Excel to monitor production dates, inventory and more. This not only helps you run your business more effectively but is instrumental in making a budget. Knowing how much money you need to set aside for manufacturing overhead will help you create a more accurate budget. Let’s define manufacturing overhead, look at the manufacturing overhead formula and how to calculate manufacturing overhead. Led by Mohammad Ali (15+ years in inventory management software), the Cash Flow Inventory Content Team empowers SMBs with clear financial strategies.
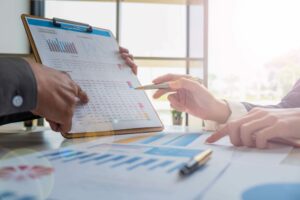
This information can be used to make important decisions about production levels and product pricing. This means that the cost of goods changes based on how many items are sold. For example, if an ecommerce business sells 500 dog sweaters, the variable costs might be $2 per sweater.
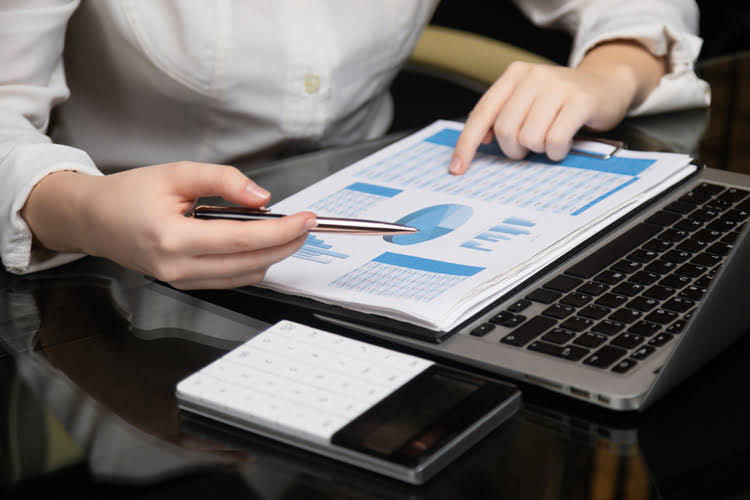
How to Reduce Manufacturing Overhead Costs:
- Other examples include legal fees and administrative expenses, transport fuel, and wages for seasonal work.
- Accurate cost calculation helps companies identify the processes or materials that are driving up manufacturing costs and determine the right pricing of products — the keys to remaining profitable.
- ABC can be more accurate than traditional overhead allocation methods, but it is also more complex and time-consuming to implement.
- A manufacturing company initially purchased individual components from different vendors and assembled them in-house.
- Including only direct or “operational” expenses in your financial plan can leave the company in a major cash crunch, as every business in every industry has to incur some overhead costs.
- After you’ve set this figure, you can calculate the manufacturing overhead rate (MOR).